Product Manufacturing
Parts + Process = Your Product
We're skilled at making good products. Our team understands that manufacturers need a computer-aided design (CAD) that's ready for production. They need engineers who can explain every detail, material, part, and how to put everything together to make sure the product works right. We also know that different products need different types of manufacturing and tools to shape each part according to your plan. We think of product manufacturing as a careful operation. Knowing how machines work, putting things together, and making parts – these are the things that make the best products stand out from the rest.
What is Product Manufacturing?
Manufacturing is the process where various components, raw materials, and machinery are brought together, shaped, and assembled according to precise instructions outlined in a CAD (Computer-Aided Design) file. The goal is to craft individual parts or put these parts together to form an entire product. This process ensures that each element is made accurately and fits perfectly, resulting in a functional and well-constructed end product.
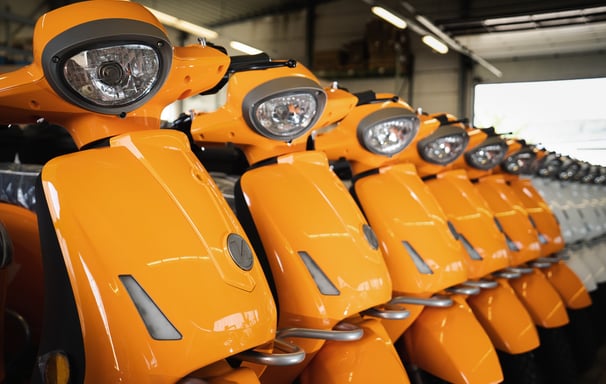
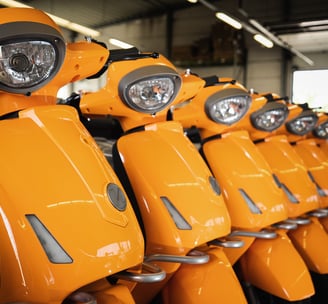
Product Manufacturing Service
At our core, we offer a comprehensive array of services to guide your product from idea to reality. Our approach encompasses a range of expertise, including 3D CAD services, mechanical engineering services, electrical product development, prototype development services, as well as manufacturing and 3D printing capabilities.
Once a finalized CAD is in hand, the next steps unfold seamlessly. We move on to evaluating materials, aligning them with your product's specifications, while simultaneously identifying the ideal manufacturers for your invention. This stage goes beyond just sourcing raw materials – it extends to the tooling process, ensuring that each component is designed in a manner that perfectly fits the overall vision of your final product.
MATERIALS SOURCING & ANALYSIS
MATERIALS / SUPPLY CHAIN
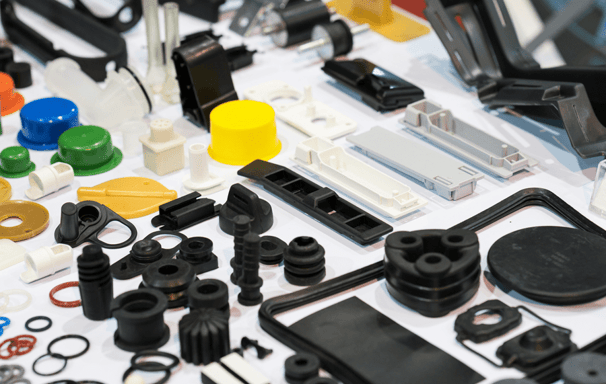
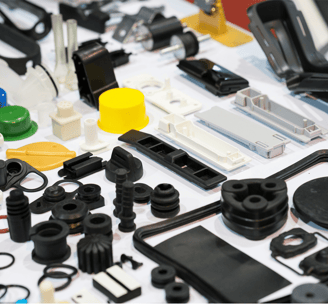
The correlation between supply and demand is a well-known concept. In the realm of purchasing everyday items, a product can be readily available, out of stock, or on backorder. Regardless of availability, the Manufacturer's Suggested Retail Price (MSRP) tends to remain relatively stable, seldom experiencing fluctuations. However, the landscape shifts when sourcing components and raw materials, as their pricing can fluctuate on a weekly, daily, or even hourly basis. This dynamism is driven by demand variations and inventory levels, influenced by the substantial volume suppliers deal with. The situation can be further compounded when considering overseas shipping variables.
MANUFACTURING ANALYSIS
MANUFACTURING DETAILS / TIMELINES / ESTIMATED COST
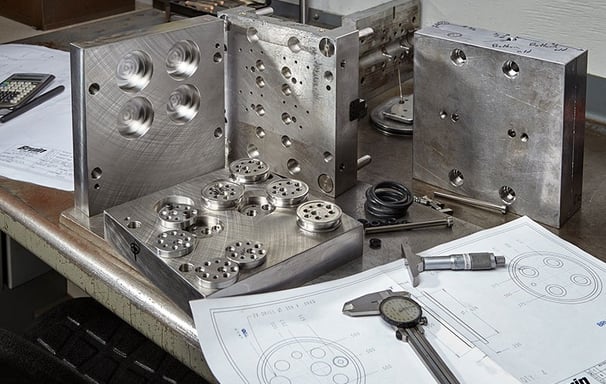
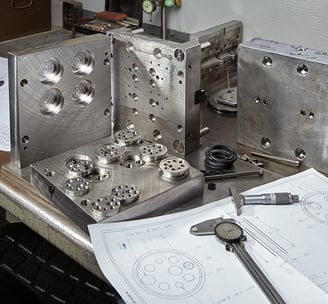
Based on the final CAD and materials selected, we’ll develop a list of potential manufacturing partners we trust for tooling the individual parts and assembling the product. We then provide this list to the client with estimated costs, projected timelines, shipping information, contact information, unit count, tooling, and any other necessary details. The objective if here is to ensure transparency so the client has full knowledge of who is manufacturing each part, where each part is being manufactured, how long each part will take to be manufactured, how and when the parts or assembled product will ship, even if the client themselves cannot be at the product manufacturing plants.
PRODUCTION MANUFACTURING
TOOLING / PRODUCTION / SHIPPING
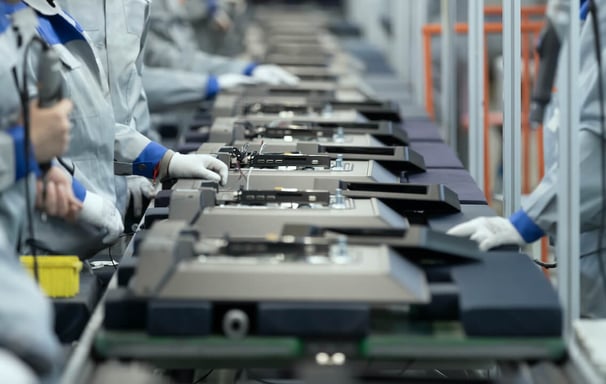
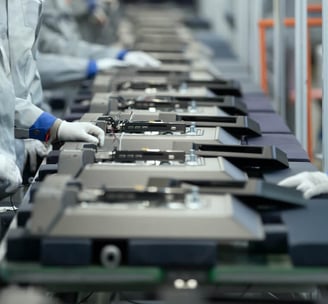
Once the manufacturing details and materials are confirmed and settled, we initiate the product manufacturing process. To ensure our clients feel secure, we also provide the choice to craft a single production unit as a sample before proceeding with larger-scale product and electronic manufacturing services. Clients have the opportunity to examine this sample unit and share their input with the Leo team and the manufacturing experts. This feedback loop helps refine the final product before proceeding with full-scale production. It's worth highlighting the significance of tooling production – the precise creation of tools that shape the parts – as well as the intricacies of shipping. Tooling ensures the product's accuracy and consistency, while efficient shipping ensures that the end products reach the desired location promptly and in top condition. All these efforts contribute to the seamless realization of the inventor's vision.
Our Manufacturing Services Can Build your Business
Tooling it Right
How are custom or proprietary parts made? The solution lies in tooling. Tooling is the method of obtaining or creating the necessary machinery components like molds, jigs, cutters, gauges, and fixtures needed for product and electronic manufacturing services. The choice of tooling process significantly impacts the part's quality, texture, longevity, and functionality, as well as the speed of production. Ill-advised tooling choices can lead to the wastage of expensive materials. Whether you're aiming for an elegant and sturdy exterior or a flexible silicone gasket with specific contours, our skilled team at Leo comprehends which tooling processes will yield optimized and premium-quality parts that align with your product manufacturing budget and deadlines.
The Key to Disrupting The Market
Regardless of whether the aim is to sell to resellers, license the product, or secure investments from backers, product manufacturing holds the pivotal key to unlocking the path to financial triumph. Prior to customers, retailers, wholesalers, distributors, or investors placing their faith in the inventor and the product, they naturally have a prudent obligation to lessen their financial uncertainty. They require evidence that the product holds genuine demand, has potential traction, or at the very least, can be successfully manufactured.
Design for Manufacturing (DFM)
For those considering larger production runs or the possibility of selling the product's intellectual property to a bigger company down the line, it's crucial to understand that the process of making a 3D printed prototype is quite distinct from producing a final product on a manufacturing line. These variations can impact both the structural and visual demands of the end product, which in turn affects how feasible it is to actually manufacture the CAD design. To ensure that the CAD design is well-suited for real production settings, beyond just 3D printing prototypes, our team must factor in potential adjustments to the shape, materials, surface finish, wall thickness, dimensions, tolerances, and other aspects of the final product that might deviate from the prototype's CAD design. We can't stress enough the importance of preparing a production-ready DFM (Design for Manufacturing) CAD design. Once production begins, making changes to the design for manufacturing consumer products – such as reworking parts or creating molds – becomes considerably disruptive and costly.
Design It Right The First Time
In the field of hardware, the launch of a new product happens only once, and that first impression needs to be exceptional. Unlike software, there's no room for patches or updates once a hardware product is in the hands of your customers. Arguably, the most pivotal phase of the product design journey is the initial CAD design, as it forms the bedrock of your creation. While adjustments can be made during product prototyping, they become notably challenging without a solid CAD model to build upon and refine. Moreover, the product design services stage usually represents a comparably lower cost within the broader product development process. So, why not lay the groundwork right from the start, especially when you have the Leo Design team at your service?
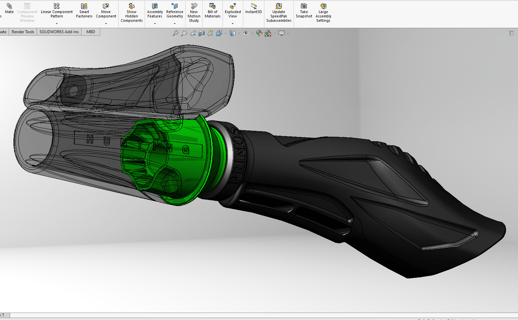
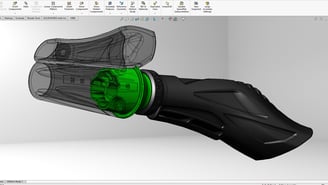
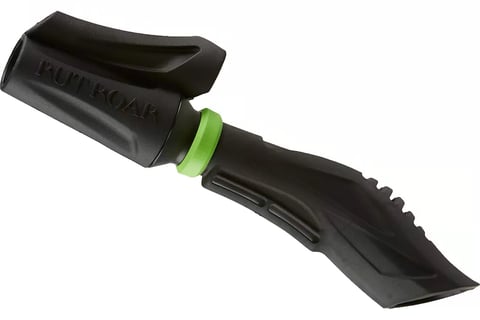
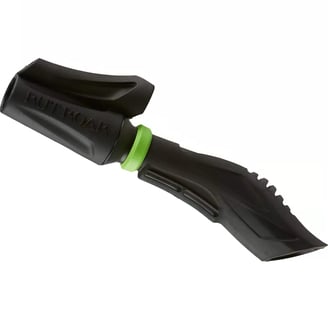
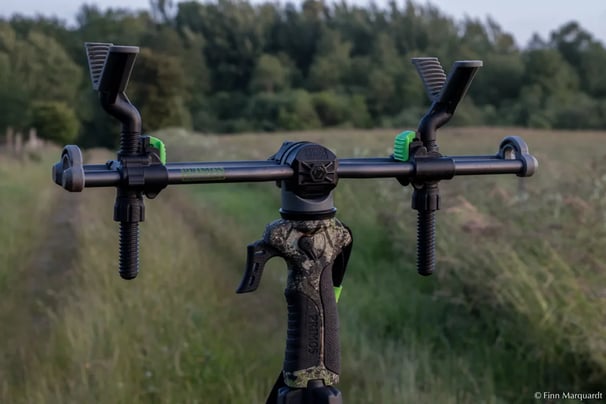
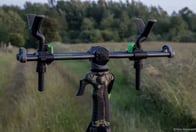
Contact us
Whether you have a request, a query, or want to work with us, use the form below to get in touch with our team.
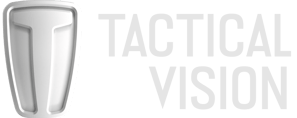
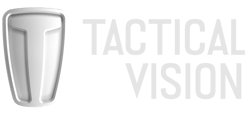
Location
1963 A. Rajabli, Narimanov, AZ1008, Baku, Azerbaijan
Hours
I-V 9:00-18:00
VI - VII Closed
Contacts
+994 50 201 0898
team@tactical-vision.com